Warum machen kleine Stückzahlen in der Umformtechnik Sinn?
In der gegenwärtigen Situation der Automobilzuliefererbranche, insbesondere jener Unternehmen, die vom Übergang zur Elektromobilität stark betroffen sind, erweist sich die S-Kurvenanalyse als wertvolles Instrument zur Beurteilung des Lebenszyklus technischer Systeme. Der Verbrennungsmotor, der sich aktuell im oberen Bereich dieser Kurve befindet, hat sein Entwicklungspotenzial hinsichtlich Leistung, Emissionsreduktion und Herstellkosten nahezu ausgeschöpft. Um weitere signifikante Fortschritte zu erzielen, ist ein Wechsel zu einem neuen technischen System unumgänglich. Die Vielfalt der diskutierten und erprobten Alternativen, darunter Elektro-, Wasserstoff- und Hybridantriebe, führt zu einer Reduktion der Stückzahlen im Bereich der konventionellen Verbrennungsmotoren. Dies stellt einen triftigen Grund für Unternehmen der Umformtechnik dar, ihre Kostenstrukturen im Segment kleiner Stückzahlen zu optimieren.
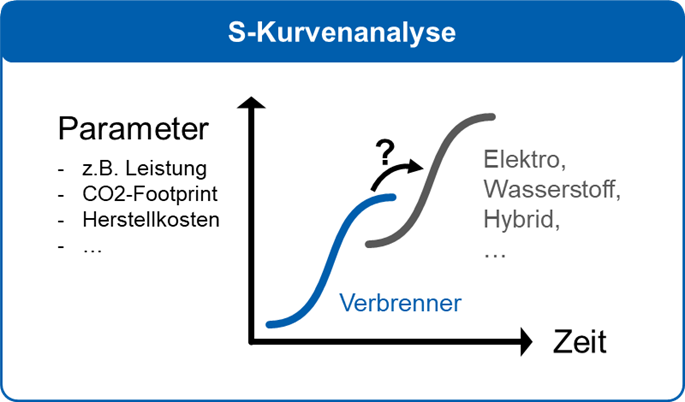
Die gegenwärtig hohe Marktdynamik liefert einen weiteren Anlass zur Kostenreduktion. Umformtechnische Betriebe sind besonders anfällig für die steigenden Energiepreise, was zu Wettbewerbsnachteilen gegenüber internationalen Konkurrenten und teilweise bereits zu Nachfragerückgängen führt. Trotz dieser Herausforderungen bieten umformtechnisch hergestellte Bauteile unbestreitbare Vorteile, wie den belastungsgerechten Faserverlauf und die ausgezeichneten Festigkeitswerte selbst bei hohen Temperaturen. Diese Eigenschaften machen sie für zukunftsweisende Bereiche wie die Elektromobilität und die Energiewende unverzichtbar. Die für solche Trendthemen charakteristischen kleineren Stückzahlen unterstreichen die Notwendigkeit einer gezielten Kostenreduktion in diesen Segmenten.
Angesichts des prognostizierten Rückgangs von Produkten im Bereich des Verbrennungsmotors müssen Unternehmen alternative Wege finden, um entgangene Umsätze zu kompensieren. Die Ansoff-Matrix bietet hierfür einen strukturierten Ansatz, indem sie vier Wachstumsoptionen aufzeigt: Marktdurchdringung, Marktentwicklung, Innovation und Diversifikation. Diese Optionen unterscheiden sich in ihrer Ausrichtung auf bestehende oder neue Märkte sowie in der Nutzung vorhandener oder neuer Produkte.
Gelingt es Unternehmen der Umformtechnik, kleine Stückzahlen kosteneffizient zu produzieren, eröffnet sich ihnen die Möglichkeit, die risikoärmste Wachstumsstrategie – die Marktdurchdringung – zu verfolgen. Traditionell haben sich viele Unternehmen in diesem Sektor auf hohe Stückzahlen konzentriert, um Wirtschaftlichkeit zu erzielen. Die aktuellen Marktveränderungen verleihen jedoch kleinen Stückzahlen eine zunehmende Bedeutung. Eine Expertise in diesem Bereich kann somit zu einem entscheidenden Wettbewerbsvorteil werden. Darüber hinaus können Unternehmen, die ihre Kosten bei kleinen Stückzahlen effektiv managen, auch neue Märkte erschließen, die bisher aufgrund zu geringer Volumen vernachlässigt wurden. Dies stellt eine weitere vergleichsweise risikoarme Wachstumsoption dar (vor allem in Relation zu Innovation und Diversifikation) und erweitert das Potenzial für zukünftige Geschäftsentwicklungen.
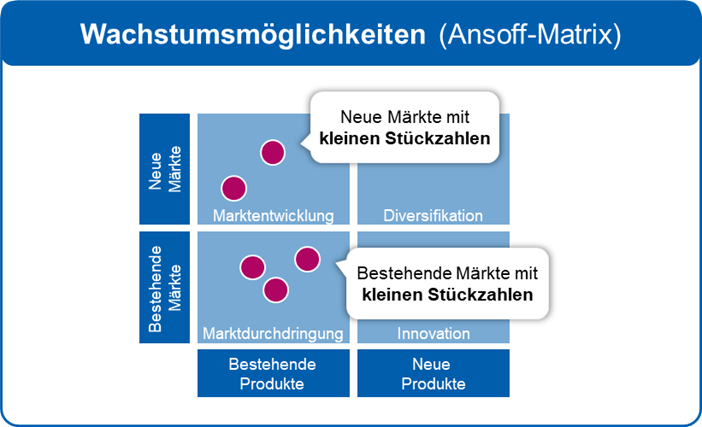
Wie können die Kosten bei kleinen Losgrößen effektiv gesenkt werden?
Um ein tieferes Verständnis der bedeutendsten Kostensenkungspotenziale bei geringen Produktionsmengen zu erlangen, empfiehlt sich eine qualitative Analyse der Stückkosten in Relation zur Stückzahl für zwei distinkte Fertigungsverfahren. Als Fertigungsverfahren A wird die zerspanende Fertigung herangezogen, die sich durch ihre bemerkenswerte Wirtschaftlichkeit bei Kleinst- und Kleinserien auszeichnet. Fertigungsverfahren B repräsentiert eine Mehrstufenpresse aus dem Bereich der Kaltmassivumformung.
Die Stückkostenkurven beider Verfahren weisen einen hyperbolischen Verlauf auf, wobei sie mit steigender Stückzahl abfallen. Der Schnittpunkt dieser Kurven definiert die Grenzstückzahl, unterhalb derer Verfahren A zu präferieren ist, während oberhalb dieser Schwelle Verfahren B den Vorzug erhält.
Zur Reduzierung der Stückkosten des Fertigungsverfahrens B stehen primär drei Ansatzpunkte zur Verfügung: die Einmalkosten, die Fertigungskosten aus Einzelzeiten sowie die Materialkosten. Die Einmalkosten, welche sich durch Division der einmalig anfallenden Kosten durch die Stückzahl ergeben, sind maßgeblich für den charakteristischen Kurvenverlauf verantwortlich. Bei geringen Stückzahlen repräsentieren sie folglich das größte Einsparpotenzial.
Die Fertigungskosten aus Einzelzeiten sowie die Materialkosten einer hocheffizienten Mehrstufenpresse sind bereits auf einem äußerst niedrigen Niveau. Anstatt weitere Ressourcen in die marginale Optimierung dieser Bereiche zu investieren, könnte eine moderate Erhöhung dieser Kosten in Betracht gezogen werden, sofern dadurch eine signifikante Reduktion der anteilig höheren Einmalkosten realisiert werden kann.
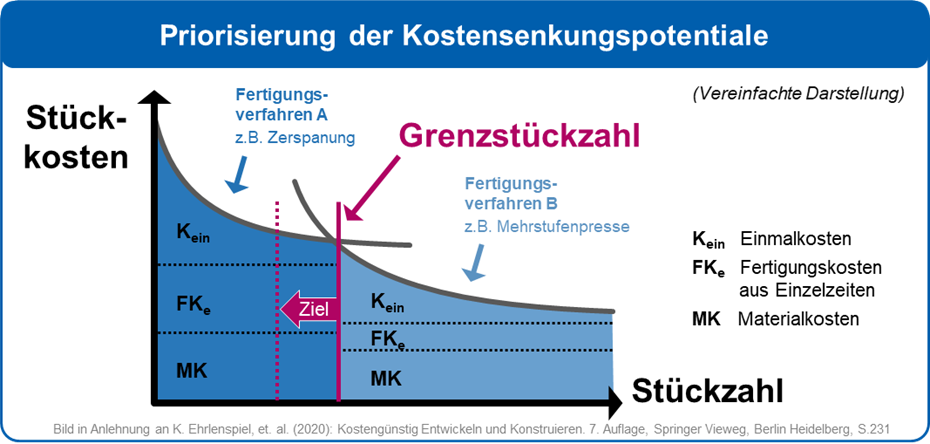
Nach Identifikation der Einmalkosten als primäres Optimierungsziel ist eine detaillierte Aufschlüsselung dieser Kostenart erforderlich. Einmalkosten umfassen sämtliche nicht stückzahlabhängigen Aufwendungen, die für Produktion und Vertrieb unerlässlich sind. Im Fertigungsbereich sind dies vornehmlich Rüst- und Werkzeugkosten. Maschinenkosten, obgleich einmalig anfallend, werden über die Fertigungskosten aus Einzelzeiten auf die Stückkosten umgelegt und zählen daher nicht zu den Einmalkosten.
Einmalkosten entstehen aber auch in anderen Unternehmensbereichen: In der Entwicklungsabteilung entstehen beispielsweise Kosten für die Konstruktion und Simulation von Umformwerkzeugen sowie für die Erstellung von Prototypen. Der Vertrieb verursacht Einmalkosten durch die Erstellung von spezifischen Angeboten und die Durchführung von Kundenbesuchen. Im Qualitätsmanagement fallen einmalige Aufwendungen für die Entwicklung von Prüfplänen und die Beschaffung von Messmitteln an.
Womit lassen sich konkret die Stückkosten verringern?
Unter den zuvor erwähnten Einmalkosten stechen insbesondere die Rüst- und Werkzeugkosten hervor. Es ist davon auszugehen, dass technologische Innovationen in diesen Bereichen erhebliche Potenziale zur Kostenreduktion bergen. Im Folgenden werden fünf Ansätze vorgestellt, die gezielt auf diese Kostensenkung abzielen.
Impuls #1: Stückzahlenabhängige Strukturen
Lernkurveneffekte spielen eine zentrale Rolle im Rahmen kontinuierlicher Verbesserungsprozesse. Oft sind es Optimierungen in Detailbereichen, die auf operativer Ebene realisiert werden und langfristig zu beachtlichen kumulativen Effizienzsteigerungen führen. Um diese Lernkurveneffekte gezielt zu fördern, können Unternehmen die Kleinserienfertigung von der Großserienfertigung separieren. Diese Trennung sollte nicht nur räumlich und technologisch, sondern auch logistisch und organisatorisch erfolgen. Dadurch erhalten die Mitarbeiter die Möglichkeit, sich in ihrem spezifischen Bereich intensiv auf die Kostensenkung bei kleinen Stückzahlen zu konzentrieren.
Impuls #2: SMED
Die aus Japan stammende Methode SMED (Single Minute Exchange of Die) bietet einen strukturierten Ansatz zur Rüstzeitoptimierung in fünf Schritten. Zunächst werden Vorgänge in interne (während des Maschinenstillstands) und externe (parallel zur Maschinennutzung) kategorisiert. Anschließend wird angestrebt, möglichst viele interne in externe Vorgänge umzuwandeln. Ein Beispiel hierfür ist das Vorwärmen von Gesenken vor dem Einbau in die Maschine beim Schmieden, was die Rüstzeit erheblich verkürzt. In den folgenden Schritten werden die Vorgänge standardisiert und optimiert, etwa durch den Einsatz von Schnellspannsystemen statt einfacher Werkzeugspannsysteme. Abschließend werden Justierungsvorgänge eliminiert und die verbleibenden Rüstvorgänge parallelisiert oder substituiert.
Impuls #3: Teilautomatisierung durch Cobots
Während sich vollautomatisierte Fertigungsprozesse erst bei hohen Stückzahlen amortisieren, bieten Cobots (kollaborative Roboter) ein erhebliches Potenzial zur Effizienzsteigerung bei kleinen und mittleren Stückzahlen. Diese Leichtbauroboter zeichnen sich durch geringere Anforderungen an die Arbeitssicherheit aus, was eine kollaborative Zusammenarbeit zwischen Mensch und Maschine ermöglicht. Ihre kompakten Abmessungen und das geringe Gewicht erlauben eine flexible Positionierung in Umformbetrieben. In Kombination mit ihrer intuitiven Programmierung machen diese Eigenschaften Cobots zu einer attraktiven Option für die Teilautomatisierung auch bei geringeren Stückzahlen.
Impuls #4: Maschinen mit geringerer Produktivität
Für kleine Stückzahlen, schwankende Nachfrage und diskontinuierliche Auslastung erweisen sich Maschinen mit geringerer Produktivität oft als vorteilhafter. Die Investitionskosten für solche Anlagen liegen deutlich unter denen hochproduktiver Maschinen. Zudem fallen die laufenden Betriebskosten, einschließlich der Umrüstkosten, geringer aus. Die erhöhte Flexibilität und einfachere Handhabung dieser Maschinen ermöglichen oft schnellere Umrüstvorgänge im Vergleich zu starren, hochproduktiven Anlagen.
Impuls #5: Gedruckte Werkzeuge
Der traditionelle Ansatz massiver Schmiedegesenke aus Werkzeugstahl folgt dem Prinzip „viel hilft viel“. Erkenntnisse aus dem Flugzeugbau über topologisch optimierte Bauteilstrukturen zeigen jedoch, dass dieser Grundsatz zwar einfach umzusetzen, aber nicht immer optimal ist. Durch belastungsgerechte Strukturen lassen sich mit reduziertem Materialeinsatz mindestens gleichwertige Ergebnisse erzielen. Die hierfür erforderliche geometrische Flexibilität kann derzeit nur durch additive Fertigungsverfahren wie den 3D-Druck realisiert werden. Diese Technologie ermöglicht zudem die Integration flexibler, oberflächennaher Kühlkanäle in Schmiedegesenke, was die Temperaturbelastung reduziert und die Standzeit des Werkzeugs signifikant erhöht. Obwohl noch Forschungsbedarf im Bereich des 3D-Drucks und der Werkzeugauslegung besteht, ist mittel- bis langfristig mit wirtschaftlich vorteilhaften Lösungen zu rechnen.
Zusammengefasst
Die strategische Ausrichtung auf kleine Stückzahlen eröffnet Unternehmen im Bereich der Umformtechnik vielversprechende Perspektiven zur Erschließung neuer Marktsegmente. Die Massivumformung zeichnet sich durch einzigartige Bauteileigenschaften aus, die das Potenzial haben, bestehende Angebote auf der Nachfrageseite zu übertreffen – vorausgesetzt, die Kosteneffizienz kann optimiert werden.
Bei der Analyse der Kostenstruktur kristallisieren sich die Einmalkosten als der signifikanteste Hebel zur Kostensenkung heraus. Unternehmen, die gezielt an der Reduzierung dieser Kostenposition arbeiten, können beachtliche Wettbewerbsvorteile generieren, die sich insbesondere bei kleinen Losgrößen manifestieren.
Um diese Kostenoptimierung zu realisieren, wurden fünf konkrete Impulse genannt. Diese Ansätze bieten Unternehmen der Umformtechnik ein breites Spektrum an Möglichkeiten, ihre Kostenstrukturen bei kleinen Stückzahlen nachhaltig zu optimieren und somit ihre Wettbewerbsfähigkeit in einem sich wandelnden Marktumfeld zu stärken.
Quellen:
H. I. Ansoff (1957): Strategies for Diversification. Harvard Business Review, 35(5), 113-124.
K. Ehrlenspiel, et. al. (2020): Kostengünstig Entwickeln und Konstruieren. 7. Auflage, Springer Vieweg, Berlin Heidelberg, S.231
K. Koltze, V. Souchkov (2017): Systematische Innovation – TRIZ-Anwendung in der Produkt- und Prozessentwicklung. 2. Überarbeitete Auflage; Carl Hanser Verlag; München
M. Leicht, N. Kopatz (2024): Studie Kleine Losgrößen – Kostensenkung bei kleinen Losen, Stückzahlen & Prototypen mittels Cross-Industry-Innovation. GCFG e.V. (German Cold Forging Group); Hagen